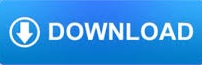
Although the performance of this early version was marginal, the development of the afterburner proceeded rapidly, and it soon became standard on most jet engines.
#Westinghouse j34 turbine series#
The initial series in early 1945 is notable because it included the first firing of an afterburner in altitude conditions. The TG–180 powered the Bell X–5, Republic F–84 Thunderjet, Northrop F–89 Scorpion, and Douglas D–558 Skystreak.ĭuring the mid-1940s, NACA researchers studied the TG–180 repeatedly in the AWT. The resulting 11-stage TG–180 (J35) initially produced 3,750 pounds of thrust. GE’s Schenectady group had been considering using an axial-flow design for its TG–100 turboprop, when the military requested them to utilize the design for a turbojet in 1943. Additional stages could be added to the axial-flow design to increase power without expanding the engine’s diameter. Each stage increased the air pressure resulting in higher energy when ignited in the combustion chamber. Axial-flow compressor engines consisted of several stages of fan-like compressor blades arranged in line. GE’s initial I–16 and I–40 turbojets employed centrifugal compressors, but the modern jet engine stemmed from the axial-flow compressor engines created simultaneously by the Westinghouse Corporation and GE’s Schenectady plant.
Summary of NACA Research on Afterburners (1956). Full-Scale Engine Research in AWT (1951). Performance of Various Types of Aircraft Engines (1947). Comparison of Turbojet, Afterburner, and Ramjet in AWT (1947). NACA Inspection Talks on the AWT (1947). AWT Investigations of Jet Engines (1945). The AWT contributed to a succession of advancements of jet engines that resulted in a tremendous surge in thrust capabilities in the late 1940s and early 1950s. The AWT’s most important contributions to the jet engines of this era involved restarting at high altitudes, afterburners and variable-area nozzles, and windmilling. Researcher then attempted to introduce various modifications to improve the performance. Most AWT test programs first determined the engine’s performance and operating range at different altitudes. Researchers operated the engines over a range of altitudes, velocities, and engine speeds. The AWT’s post-war research focused on the improving engine performance at high altitudes and refining components such as the afterburner. They also studied other types of engines, including the turboprop and ramjet. NACA researchers conducted extensive testing of General Electric’s (GE) TG–180 and TG–190 and Westinghouse’s 24C and J40 during this period. For most investigations, the airflow was ducted directly into the engine inlets. The NACA upgraded the Altitude Wind Tunnel (AWT) several times during the 1940s and 1950s to keep up with the increasingly more powerful jet engines. With the end of World War II in the fall of 1945, the laboratory ( renamed the Lewis Flight Propulsion Laboratory in 1948) underwent a major reorganization to focus on the new turbojet and missile technologies. The AWT’s post-war testing and improvement of axial-flow turbojet engines was the facility’s most enduring contribution to the aerospace field. Home > Glenn Historic Facilities > Altitude Wind Tunnel Post-war Engines Researchers studied the TG-190’s operating characteristics, inlet performance, an experimental fuel, and afterburner configurations n the AWT ().